

He currently owns four license agreements and six US patents in the field of semiconductor manufacturing. His research interests are primarily in the areas of queueing theory, with applications in the performance evaluation of supply chains and manufacturing systems. dissertation was awarded third place for the IIE Pritsker Doctoral Dissertation Award in 2010. Theory of Constraints provides a set of holistic processes and rules, all based on a systems approach that exploits the inherent simplicity within complex. Before joining NTU, he was the CTO and founding team member of a startup company in the US. He has guided the development of scheduling and dispatching systems at the Taiwan Semiconductor Manufacturing Company and ramped up a 300 mm DRAM fab for Inotera Memories. Goldratt defines the Theory of Constraints as 5 + 1 steps. He has 10 years of experience in the semiconductor industry, from a consultant to an IE manager. Theory of constraints is an approach to identifying the most important limiting factor (ie constraint) that prevents any system or process from meeting its. degree in industrial and systems engineering from Georgia Institute of Technology. degree from the University of California at Berkeley, and Ph.D. degree from the National Tsinghua University, M.S. The following five steps are designed to help you discover constraints early in order to minimize or eliminate them. These are problems to be solved, before you can move on to the next problem. Kan Wu is an assistant professor in the School of Mechanical & Aerospace Engineering at Nanyang Technological University. The Theory of Constraints is about finding points of failure, or points of weakness. According to the GPOOGI, the managers of production systems would be able to make optimal decision during the continuous improvement process. The findings indicate that we should consider the dependence among stations and the cost of improvement options during productivity improvement and should not simply improve the system bottleneck according to the conventional TOC. It shows that improving a frontend machine in a production line can be more effective than improving the throughput bottleneck. Incorporating the system variability and improvement costs, the Generalized Process Of OnGoing Improvement (GPOOGI) is developed in this study. We show that, in stochastic settings, the conventional TOC may not be optimal, and a throughput bottleneck should be considered in certain types of machines at the planning stage. In manufacturing, the constraint is often referred to as a bottleneck.
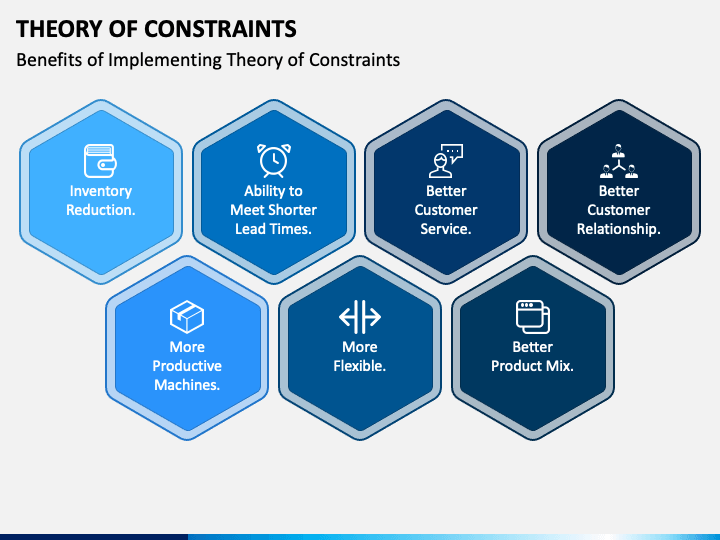
This article generalizes the concept of TOC to stochastic settings through the performance analysis of queueing systems and simulation studies. The Theory of Constraints is a methodology for identifying the most important limiting factor (i.e., constraint) that stands in the way of achieving a goal and then systematically improving that constraint until it is no longer the limiting factor. Although it is intuitive and easy to understand, its conclusions are mainly derived from deterministic settings or based on mean values.
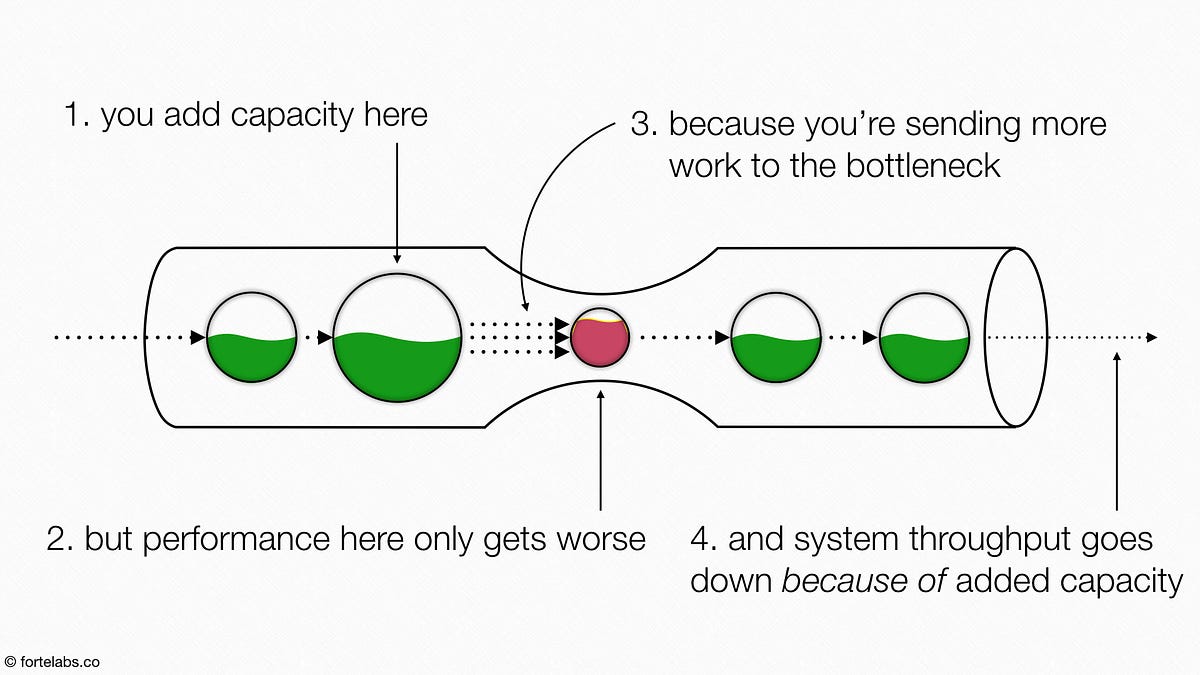
The Theory of Constraints (TOC) was proposed in the mid-1980s and has significantly impacted productivity improvement in manufacturing systems.
